【摘要】随着当前生活水平的逐渐提高,人们对汽车的需求量越来越大,然而对汽车的品质要求也越来越高。主机厂在提高汽车品质方面,冲压工艺的完美是不可缺少的一部分,冲压工艺师往往通过一些方法来保证冲压工艺的完美性,如在冲压拉伸过程中使用到底标记;为保证装配的正确性,冲压件增加左右件标记;为达到钣金件的追溯,使用批次标识等,本文中将重点介绍冲压工艺标识分类。
1 引言
要想做好汽车冲压工艺,细节是不容忽视的。要想做好冲压拉伸工艺,到底标识是不可忽视的。要想做到钣金件的可追溯性,批次标识是不可忽视的。除此之外还存在左右件标记等,本文对冲压工艺的标识进行了分类并进行详细讲解。
2 汽车冲压工艺标识的3类分类
2.1 到底标记
(1)定义。
刻印制件上的标记,主要用于检测汽车冲压钣金件是否拉深、成形到位。
(2)类型。
到底标记一般为圆形,验证冲压是否到底,通常要求圆形标记大于3/4为合格,如图1所示。
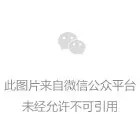
(3)技术要求。
a.一般设置于废料处(非产品处),并与板料较晚接触的平面部位。
b.对角线长大于等于500mm的产品设置2处且距离不宜太近,对角线长小于500mm可设置一处。
c.双动/单动拉伸模安装在凹模凹面上,尽量在水平平面上,且与平面垂直,或型面 Φ25mm以上平台面上。
d.到底标记安装在产品成形后,形状不再变化的位置,不设置在易起皱的压料面及材料移动的位置。
e.用螺钉固定,比安装面高0.25mm,如图2所示。
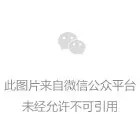
f.到底标记要沿着制件型面的法向设计、加工,角度取整(以1°为单位)。
g.必须确认位置是否与D/L图相同。
2.2 数字及字母标记
(1)定义。
数字及字母标记除验证冲压是否到位外,还用于制件的区分以及装配位置的确定。
(2)分类。
a.字母标记:如图3所示字母左右标记用于区分左右件;图4字母前后标记,为某汽车厂顶盖外板,Q为前的意思,在焊接装配过程中此面装配于车身前部。
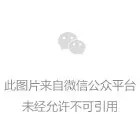
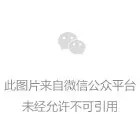
b.数字标记:如图5数字标记,为某汽车厂顶盖加强梁三,数字3表示此制件为顶盖的第三个加强梁(从前至后依次排序)。
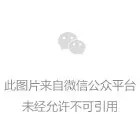
(3)技术要求。
a.设置在产品的表面,不影响焊接搭接面精度及美观的位置。
b.对角线长大于等于500mm的产品设置2处且距离不宜太近,对角线长小于500mm可设置一处。
c.双动/单动拉伸模安装在凹模凹面上,尽量在水平面上,且与平面垂直,或型面Φ25mm以上平台面上。
d.安装在产品成形后,形状不再变化的位置,不设置在易起皱的压料面及材料移动的位置。
e.用螺钉固定,比安装面高0.3mm,如图6数字及字母螺栓安装图示。
f.要沿着制件型面的法向设计、加工,角度取整(以1°为单位)。
g.必须确认位置是否与D/L图相同。

2.3 冲压钣金件批次标识
(1)定义。
用于冲压钣金件试生产/生产过程中问题跟踪及质量问题追溯,施加在钣金件上的字符(由字母或数字组成的),来表示钣金件的生产(变更)批次。
(2)技术要求。
a.基本要求。
批次标识组成:
①批次标识由16个字符组成(也可增加或减少字符,本文将以16位字符为例进行详细介绍),依次为产品制件号、批次标识号。例如:某车型C柱加强板本体(5401513XLC02A)第一次生产,批次标识为:5401513XLC02A-01,如图7所示。
②从01依次标记,如某车型左C柱加强板本体第一次模具变更后进行生产,批次标识应为:5401513XLC02A-02。

③无法满足16个字符的,只标记16个字符的后四位,例如某车型左C柱加强板本体(5401513 XLC02A)第一次生产,批次标识为A-01。
④当变更较多第15-16位生产批次号无法满足标记时,可将第14位的分隔符变更为数字和15-16位一同作为批次号,如某车型左C柱加强板本体101次变更,批次标识应为:5401513XKR02A101。
⑤批次标识压印需参照图8所示进行排列,阿拉伯数字及英文用采用“Arial”常规字体。

b.批次标识压印范围。
批次标识应在钣金件平面区域进行压印,如图9左图所示,优先考虑压印在凸面区域的平面上,无法满足凸面区域时,则选用图9右图所示,压印在凹面区域平面上。压印字符的多少根据面积的大小优先选择1排16个字符、2排每排8个字符、1排4个字符(也可依据压印的面积、模具标准件大小进行其他排列)。

①当标记16个字符(16×1-3×2)即1排16个字符,字高3mm,字宽2mm时,尺寸要求:图9凸面区域尺寸≥10×43mm,图9凹面区域尺寸≥20×73mm。
②当标记8个字符(8×2-3×2)即2排每排8个字符,字高3mm,字宽2mm时,尺寸要求:图8凸面区域尺寸≥25×27mm,图2凹面区域尺寸≥40×57mm。
③当标记4个字符(4×1-5×2):即1排4个字符,字高5mm,字宽2mm时,尺寸要求:图9凸面区域尺寸≥10×27mm,图9凹面区域尺寸≥20×57mm。
批次标识压印深度H:当产品料厚t≥0.8mm时,H=0.3mm;当t<0.8mm时,H=0.2mm,检测方式:目视,批次标识在产品上100%显示。
(3)批次标识压印面的要求。
a.车身所有冲压钣金件均需压印批次标识,压印位置在产品图纸中体现,优先遵从原则:人在白车身外部或白车身内部的可视区域且易于识别的位置;不应出现在外A面、匹配面、包边面、GD&T的基准面上,尽量不要压在冲压件的侧壁上。
b.字体高度方向倾斜度小于1°,如图10所示,字体宽度方向倾斜度小于5°,如图11所示。

c.侧围、翼子板等外板在不影响外观的位置进行压印。
d.产品推荐压印位置如图12、图13所示。
(4)变更要求。
a.达到追踪效果,批次标识从产品首次生产时开始压印。


b.根据生产的不同,车型SOP前每批次冲压钣金件均需变更批次标识。
c.SOP后模具状态发生变化(包括但不限于产品形状、材质、修模等导致模具状态变化的),需变更一位批次标识。
(5)凸模座要求。
a.批次标识凸模座总成图如图14所示,尺寸从表1进行选取。


b.为确保安全,当标记凸模反面部件硬度<30HRC时,需采用冲击垫板如图15所示。冲击垫板尺寸从表2中进行选取。
(6)凸模要求。
a.字高3mm标记凸模如图16所示。


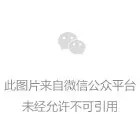
b.字高5mm标记凸模如图17所示。
c.批次标识凸模座安装如图18所示在冲击垫板上预留1个Φ2.5H12mm的孔用来插入弹性圆柱销,配合安装凸模座。
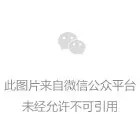
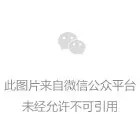
3 结论
(1)问题发生之后我们并没有盲目的去整改模具,而是通过理论分析制定方案,寻找出问题的真因并经过模拟验证,确认方案可行后实施确认。
(2)理论分析需要与现场实践相结合,利用软件分析辅助现场实施,利用现场操作验证理论分析,理论结合实践,实践总结真理。 |